I. What are the ways of harness pressure welding process? Harness pressure welding methods are diffusion welding, high-frequency welding, cold pressure welding, ultrasonic welding. 1, diffusion welding: in a certain temperature and pressure will be welded material welding surface contact with each other, through the microscopic plastic deformation or through the weld surface produces a small amount of liquid phase and expand the physical contact to be welded surface, so that the distance away from the up to (1 ~ 5)x10-8cm (so that the gravitational force between the atoms play a role in the formation of a metal bond), and then after a longer period of time between the atoms continue to diffuse, mutual penetration to achieve a metallurgical combination of a welding method. ), and then after a long period of time of the continuous diffusion of atoms between each other, mutual penetration, to realize the metallurgical bonding of a welding method. Obviously, for ordinary wire harness welding, the use of diffusion welding cost is too high. 2, high-frequency welding: is a solid resistance heat as an energy source. Welding the use of high-frequency current in the workpiece generated by the resistance of the heat so that the workpiece weld area surface heated to melting or close to the plastic state, and then apply (or not) the top of the forging force to achieve the combination of metals. Therefore, it is a solid-phase resistance welding method. High-frequency welding according to high-frequency current in the workpiece to produce heat can be divided into contact high-frequency welding and induction high-frequency welding. Contact high-frequency welding, high-frequency current through mechanical contact with the workpiece and into the workpiece. Induction high-frequency welding, high-frequency current through the workpiece external inductor ring coupling effect and produce inductive current in the workpiece. High-frequency welding is a highly specialized welding method, which should be equipped with special equipment according to the product. High productivity, welding speed of up to 30 m / min. mainly used in the manufacture of pipe longitudinal seam or spiral seam welding. Obviously, for small wire harness, high-frequency welding is not applicable. 3, cold pressure welding: pressurized deformation, the workpiece contact surface of the oxide film is destroyed and extruded, can purify the welded joints. The added pressure is generally higher than the yield strength of the material to produce 60 to 90% of the deformation. Pressurization can be slow extrusion, rolling or impact force, can also be divided into several pressurization to achieve the desired amount of deformation. Cold press welding is simple to equip due to no heating and no filler. Welding of the main process parameters have been determined by the size of the mold, so it is easy to operate and automation, welding quality and stability, high productivity, low cost, no flux, joints will not cause corrosion, welding joints, the temperature does not rise, the material crystallization state remains unchanged. Particularly suitable for dissimilar metals and hot welding method can not be realized by the welding of some metal materials and products.
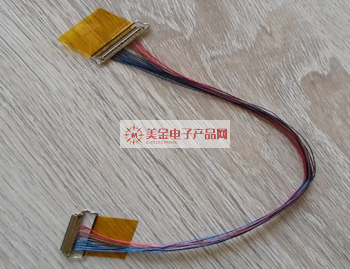
-Third, on the U.S. dollars electronic products network platform related to the introduction and sales of products brief: U.S. dollars electronic products network - a professional agent / production / sales of a variety of {connectors | wiring harness | wire and cable products }; if you have a related [connectors | wiring harness | wire and cable products] purchasing / sourcing needs or would like to buy / to understand what we can provide connectors | harness | wire and cable products solutions, please contact our business staff below; If you have related [connector | wire harness | wire and cable production] sales / resources and promotion needs, please click on the ¡¡ Business Cooperation ← ¡" to discuss with a person!