EV has become a national strategy, and it is planned to reach sales of 5 million vehicles in 2020. Together with the construction of foreign markets and charging stations/piles, a large market will be opened up. As the main component of telex, EV cable is the carrier of power signal transmission and plays a huge role. EV cables are mainly divided into cable materials for charging piles/stations and high-voltage cable materials in vehicles. Due to high voltage, high current and harsh use environment, high safety specifications and use requirements are put forward for cable materials.
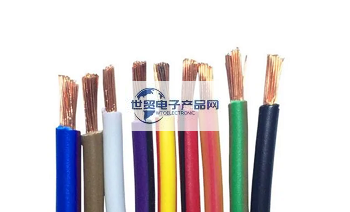
-------------------------------------------------------------------------------------------------
1. Development status and future development direction of EV cable materials • 1.1 Classification and standard charging pile/station cable: CQC1103; TUV1908; UL62; EN50620; IEC62821 Interior High Voltage Line ISO6722 DECRA K175; GB/T12528
1.2 CQC/TUV charging cable material requirements and development status: The material is cross-linked elastomer, TPE, TPU, HF-XLPE, PVC (of which TUV does not have PVC material) • The mainstream is TPE, TPU • Requires oil resistance, tear resistance, weather resistance, water resistance, acid and alkali resistance, high and low temperature resistance, soft • The insulation resistance requirement of insulating materials is higher CQC than TUV • The sheath material TPE material CQC tear resistance requirement is 25, and TUV is 15 • The materials currently made in China basically meet the certification requirements. However, some manufacturers have shortcomings such as high hardness, risk of cracking caused by tear-resistant NG, and easy precipitation of dust. During use, further adjustments need to be made according to customer requirements. Zhongxu has solved these problems.
1.3 UL charging cable material requirements and development status: It is required to be in accordance with the UL62 standard of power cord, and the material is PVC, TPE, etc. • The insulation has water capacitance and stability factor requirements • The sheath must be resistant to-40-105 °C, ASTM2 # oil, UV resistance, 150 degrees 2000g thermal deformation, hot and cold shock, VW-1 flame retardant and other tests. • There are no special environmental protection requirements • At present, manufacturers mostly use nitrile composite elastomer from Singapore SPC, and domestic manufacturers have also developed it, and the quality is similar. 1.4 EN/IEC charging cable material requirements and development status: The standard is basically the same, unfinalized, and EN50620 is the main introduction. As GB generally adopts IEC standard, IEC generally adopts EN standard, it is possible to set GB based on this in the future. The electrical performance requirements of insulation materials are high, and TPE or cross-linked elastomer is adopted. The sheath adopts TPU or cross-linked elastomer, which has high oil resistance requirements. ASTM2 # requires low smoke and halogen-free. At present, the sheath generally adopts BASF's TPU and domestic insulation materials are well developed. At present, it is in the lead in China. Especially TPU sheath, pH and conductivity are OK.1. 5 high-voltage line materials. II. Problems that are easy to occur in the development of EV cable materials. Due to the high-voltage electrical system adopted by EV, high requirements are put forward for cable materials, and improper selection will cause serious consequences. 2.1 It is not tear-resistant and easy to crack. Because the internal space of EV is limited, the bending radius of the cable is small, and the temperature rises a lot due to high current and high voltage. At present, flame retardant TPE materials generally contain polyphenylene ether, which has poor stress cracking resistance and notch growth resistance. 2.2 Not resistant to oil. Since many new energy vehicles today are hybrid, and most charging stations are built next to gas stations, they are gasoline resistant to high-voltage line materials and charging station cable materials. Diesel, engine oil requirements. If the material is not resistant to oil, there is a hidden danger of failure after oil contamination in use in the future. 2.3 Non-wear resistance 2.4 Non-rolling resistance 2.5 High hardness is not easy to construct 2.6 Precipitation frost spray 2.7 Wire bulging belly 2.8 Poor electrical performance 2.9 Poor flame retardant 2.10 Not resistant to hot cutting 2.11 Poor water resistance and weather resistance 2.12 Not resistant to high temperature 2.13 Low temperature hardening 3. Corresponding solutions to the problem, cracking resistance problem • Reasons: 1. Tear strength is too low, and it is easy to cause longitudinal cracking of cables to above 15KN/M 2. High temperature cracking thermal shock NG hot penetration NG aging NG and other solutions: Improve the material heat resistance 3. Low temperature cracking thermal bending, cold punching NG and other solutions: Improve the material heat resistance 3. Low temperature cracking and cold bending, cold punching NG and other solutions: Improve the material heat resistance through the combination of antioxidants. 6. Flame-retardant NG adopts high-efficiency flame-retardant system, such as ADP + carbon-forming resin CR1800 and other oil-resistant NG solutions: 1. The base material adopts oil-resistant rubber, such as hydrogenated nitrile rubber and acrylate rubber. 2. Adjust the balance of softness and hardness and oil resistance of the material through IPN structure. 3. Micro-crosslink the material to improve oil resistance. 7. Precipitation and frost spray. 4. Development direction of EV cable materials 1. Environmentally friendly, low-smoke and halogen-free Tesla requires halogen-free UL62 wire 2. High-voltage wire material resistant to high and low temperatures-55 _ 150 °C, fast-charging wire material at 125 °C 3. In order to improve the impact of short-circuit temperature, the insulation adopts high-temperature resistant XLPE or cross-linked elastomer 4. Soft 65A sheath, 80A large square high-voltage wire material 5. Tear resistance and cracking resistance requires tear resistance greater than 40 6. High flame retardant bundle flame retardant ICE60332-3C7. Wear resistance and rolling resistance 8. Thin wall and high strength to reduce the weight of the cable 9. Slingshot wire to facilitate the placement of the charging cable 10. Luminous cable, which can play a warning role at night
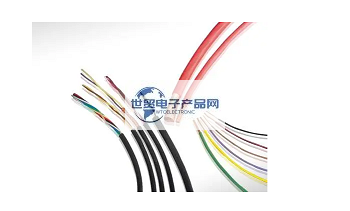
-------------------------------------------------------------------------------------------------5-------------------------------------------------------------------------------------------------------------------------------------------------------------------------------------------------------- If you have related [connector wiring harness and cable production] purchasing/purchasing needs or want to purchase/understand which connector wiring harness and cable product solutions we can provide, please contact our business staff below; If you have related sales/resources and promotion needs of [Connector Wiring Harness and Cable Production], please click "→ Business Cooperation ←" to negotiate with a dedicated person!